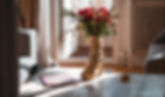
Tabi Vase
Year
2023
Fields
Product Design
Industrial Design
Overview
A narrated exploration of the surrounding culture
This project is based on my perspective and research as an exchange student in Genk, Belgium. Over the course of two months, I utilized interaction design thinking in a product design sphere to explore both the obvious and lesser-known cultural aspects of the area. My goal was to inspire a shared appreciation for Genk’s unique story and to foster an intimate connection between the area, its history, the potential future, and individual experience through a product.
Overview

Problem statment
Revitalizing Genk's Cultural Identity
The project addresses the neglect and under-appreciation of Genk's cultural and historical significance, as expressed by residents. Despite its rich heritage and deep-rooted Catholic tradition, the area's unique identity remains largely overlooked. To tackle this, the research adopts the framework of the traditional phrase "Something old, something new, something borrowed, something blue," aiming to explore and revive the city's cultural essence.
The project focuses on four key narratives—history, nature, fashion, and sport—to uncover and weave together these elements to create a comprehensive and meaningful representation of Genk, bringing its cultural identity back to the forefront.

Key Points
Something Old
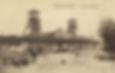
A Legacy Carved in Stone
Although abolished today, the mining industry stands as a pillar of Genk’s history. The city's development and cultural landscape are deeply intertwined with coal mining. This legacy of resilience and community spirit continues to influence Genk’s identity and growth.
Something Borrowed
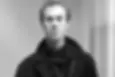
Artists and Innovation
Artists and innovators from other parts of the country have long been a core part of Genk. Even though Maison Margiela is not a local brand, one of its founders, Martin Margiela, was born in Genk. His avant-garde fashion and design ethos add a layer of cultural prestige, reflecting a spirit of ambition and innovation that is somewhat forgotten today.
Something New
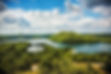
A Green Oasis
Genk is a city where urban life and nature coexist harmoniously with a unique natural landscapes in and around the city, the scars of mining can be see all over the area including the Hoge Kempen National Park, which offers a serene escape and reflect Genk’s commitment to preserving nature for the future.
Something Blue

A Unity in Sport
The most obvious cultural aspect of Genk is the Football Club, KRC Genk which to me symbolizes community and pride for the city. The club’s successes and challenges foster a sense of unity among residents, highlighting the importance of sports in building social cohesion and local pride.
Keeping in Line with Multiple Design
The biggest challenge was to incorporate these narratives into a design that both provokes thought and fosters a sense of belonging, a task that initially seemed elusive. It took considerable time, ideation, and multiple sketches to successfully integrate even a single narrative into a functional daily item, let alone combine all narratives into one cohesive piece that felt interesting. The final design needed to be meaningful and reflective of the insights gained and practical in terms of production, with a target quantity of around ten items. This approach aligned with the course’s emphasis on multiple designs and led me to explore the concept of a daily item as it would be both attractive and marketable, ultimately suitable for sale at a market in the course conclusion. In the end, the idea of a ceramic vase was established, which successfully integrated all the narratives into the design.

Step-By-Step Development
CAD Drawing
The initial design phase involved creating detailed CAD drawings to ensure precision and functionality. This step was crucial in visualising the final product and making necessary adjustments before production began to smooth out the transition between the digital and physical product while also being able to see the concept in a 3D environment as opposed to a 2D sketch. The initial sketch of a foot acted as a guide on which the boot was constructed around, this was crucial to have a shoe that was somewhat close to looking proportional. The boot was constructed using free form through multiple steps, when done a negative mould was created from the boot to see what steps to take to create one for the next coming step.

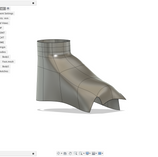
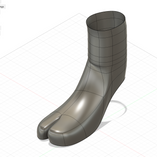

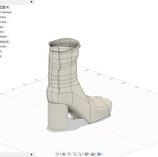
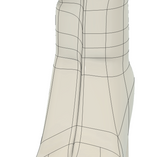


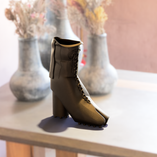
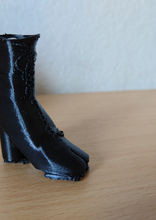
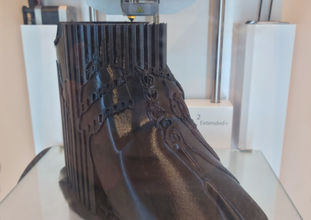


3D Printing
I utilized 3D printing to create prototypes and subsequent templates for mould-making. This approach allowed me to test and refine the design while minimizing unnecessary waste. It was a crucial step in determining whether the design would work in reality, as there was uncertainty about how well the concept would translate into a physical print. Given the refined nature of the CAD sketch, only three versions were created. Two of these versions failed, which was anticipated, but the issues were later resolved through adjustments in the slicing program and tweaks in Fusion 360. The final print was then manually sanded and cleaned to remove imperfections and residues.
Plaster Moulding
As the method of slip casting was chosen for producing the vases due to its efficiency in creating multiple pieces, a multi-part plaster mould needed to be crafted, which allows for easy reuse while preserving the integrity and details of the design. To create the mould, clay was applied to specific areas of the boot to section off where the connections of the mould pieces should be, but also to address issues with small details on the boot that were discovered during this process. The boot was then coated with soap and grease to ensure it could be easily released from the mould when the slip casting was done. The final mould was cast in three separate parts, ensuring ease of use in production.





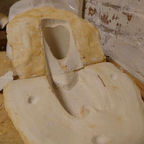
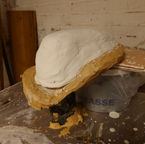
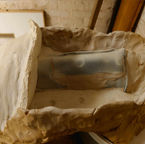

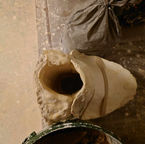

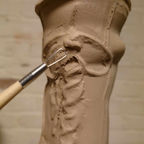




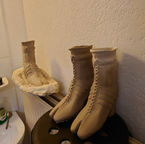

Slip Casting
Slip casting is a ceramic production process in which a liquefied clay mixture, known as slip, is poured into a plaster mold. As the mold absorbs water from the slip, a layer of solid clay forms against the mold's surface. Once the desired thickness is reached, the excess slip is poured out, leaving the molded clay to dry and take shape. While this process is effective in preserving the details of the piece, some intricate parts required additional work with hand tools afterward, which was the most time-consuming aspect of the process. Once the detailed adjustments were completed, the pieces needed to dry for approximately two weeks.
Glazing
Once dry, I fired the pieces initially to harden the clay and prepare them for glazing. This first firing, known as bisque firing, strengthens the pieces and makes them less fragile, allowing the glaze to adhere properly. Afterward, I created my own glaze by combining different components, resulting in three distinct glazes with varying degrees of success. I then applied a thin layer of this glaze mixture using compressed air.


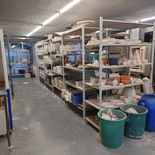




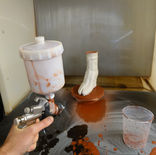
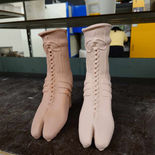

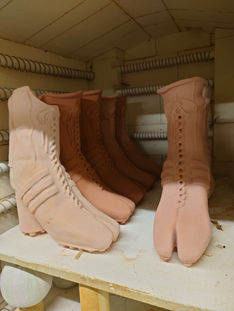

Firing
To complete the process and achieve the finished product, I fired the pieces one final time after glazing, which fused the glaze to the surface and finalized the appearance and achieving the desired finish and durability. With the help of a skilled professional, each piece was fired to perfection, resulting in a high-quality, long-lasting product. However, some issues arose during this stage, as a few pieces became stuck to the oven floor due to the glaze, causing some of the studs on the bottom of the boot to become misshaped. Fortunately, this did not affect the overall functionality of the vase and I ended up with seven vases in the end.

Outcome & Next steps
Market
Seven pieces in total were created and sold at a market for 50 euros each. The response from buyers was overwhelmingly positive. Many were particularly intrigued by the story embedded in each piece, which reflects the cultural and historical essence of Genk. The narratives of history, nature, artistry, and sports resonated with the buyers, creating a deeper appreciation for the city's unique identity. The market not only served as a sales platform but also as an avenue for gaining feedback from the community for which the product was created, allowing for further insights and validation of the previous research conducted.
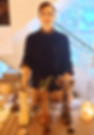
Final Mass-Production Plan
The final step of the project involved developing a plan for a mass-production phase. This included refining the vase design by simplifying its shape such as removing sharp edges and inaccessible parts to improve mould-making and production efficiency. The mould design was adjusted from three to five pieces to enhance consistency and ease in production. Extensive research, including web searches and interviews with professional ceramists, was conducted to identify the most effective methods for mass-producing this ceramic piece. This research informed the creation of finalized CAD sketches of the vase, mould, and technical drawings with precise measurements, ensuring both accuracy and scalability for large-scale manufacturing.
Conclusion to the journey
This project has been what I would describe as a "project of firsts." It marked my first time working with CAD, ceramics, and product design. Despite the steep learning curve, each challenge provided valuable insights and skills that contributed to the final outcome. From initial ideation and sketching to the intricacies of 3D printing, mould-making, and slip casting, every step was a learning experience that pushed me beyond my comfort zone. The journey was filled with unexpected obstacles, like the issues with the final firing, but these moments taught me resilience and problem-solving. In the end, this project not only resulted in a tangible, marketable product but also in significant personal and professional growth.
